What Carbide Inserts Are Made From
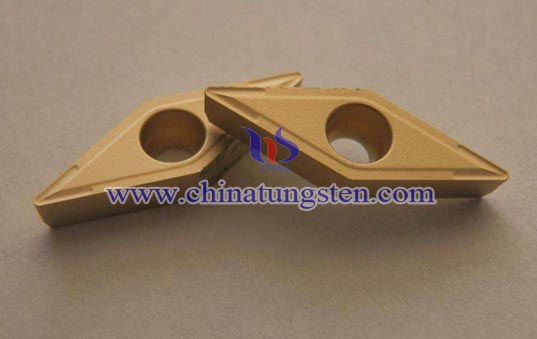
How Carbide Inserts are made?>
Manufacturing and machining shops that rely on tungsten carbide inserts for high speed tooling typically go through thousands of inserts each year. Machine operators work with many inserts each day, relying on their complex combination of chemistry and geometry to provide the cutting edges needed for precision, high speed production. Understanding how carbide inserts are made and how the insert manufacturing processes influences their capabilities can help machine operators and manufacturers better understand their tools and overall processes.
What Tungsten Carbide Inserts Are Made From?
Tungsten carbide inserts consist of cemented carbide, which is made from a combination of cobalt and tungsten carbide. Tungsten carbide's hard particles within the insert provide the insert with its qualities of hardness, and cobalt acts as the binding agent, holding the materials solidly together. The size of the tungsten grains being used affects the insert's hardness; larger grains (3-5 microns) result in softer, more quickly worn insert materials, while small grains (less than 1 micron) result in extremely hard, wear resistant inserts. The harder the insert, the more brittle it will be. When machining metals of exceptional hardness, harder inserts with smaller grains are typically used, while softer inserts are used most often in machining processes with interrupted cuts, which call for less brittle, tougher insert materials. The ratio of cobalt to tungsten carbide also influences carbide inserts' hardness levels; cobalt is softer, so the more cobalt an insert contains, the softer it will be.